Greetings to all. February arrived with thunder. With a constant parade of cyclones marching up the coast the ground was becoming saturated. The creek behind the house was nearly full, a rushing torrent, almost filling a 12’ culvert where it goes under the road. But the thunder I heard one morning two weeks ago shook the entire house. It sounded more like a train wreck. Rushing out on the front deck, expecting to see a 747 in my field, I saw nothing. Okay, check the back… Going out back I saw it. One of my biggest trees, a 300 plus year old white oak, 5’ thick at the base had decided to give up. This was a decent sized tree when the Indians lived in this valley and here she was laying on her side. I was sad to see this beautiful tree go but then it struck me, I had just been wondering where I was going to get the white oak for Theresa’s frames. There is a log here that is 5’ thick and 30 ft long. All I need is a crane and a sawmill. And yes, I know, I need a bigger chain saw. Unfortunately, though it will take several hours a day for several months to clear this mess. Thank heaven it didn’t fall on the shop. It would have crushed it to splinters. Perhaps I should be more specific about what I wish for.
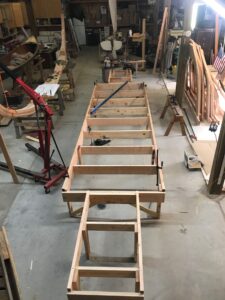
Aside from the tree, taking a huge bite out of my day, I have been making progress with Theresa. It is slowly becoming evident to me that if I keep up the same glacial speed which has gotten me this far in 2 years I should be ready to launch in the next 20 years or so. This disquieting deduction came to me one day as I was sitting admiring my work, that I had built my whole house with only 1 helper and also all of the cabinets and some of the doors together with all the electric, plumbing and tile work, and more, and it had only taken me a year and a half. Yet in 2 years, with Theresa, I have barely managed some artwork on the floor and a keel. The earth-splitting revelation continued: What factors contribute to this? I wondered. Could it be, a) My land requires too much maintenance or b) My chair in the shop is way too comfortable or C) I’m enjoying the building of it more than the prospect of getting it done. And so, Theresa and I got together and we decided that something had to change. I vowed to stop asking myself “what’s the worst that can happen” before I make every cut and she will try to explain more clearly what her special needs are and I will try to be more responsive. Sometimes negotiations are required to keep the project moving forward.
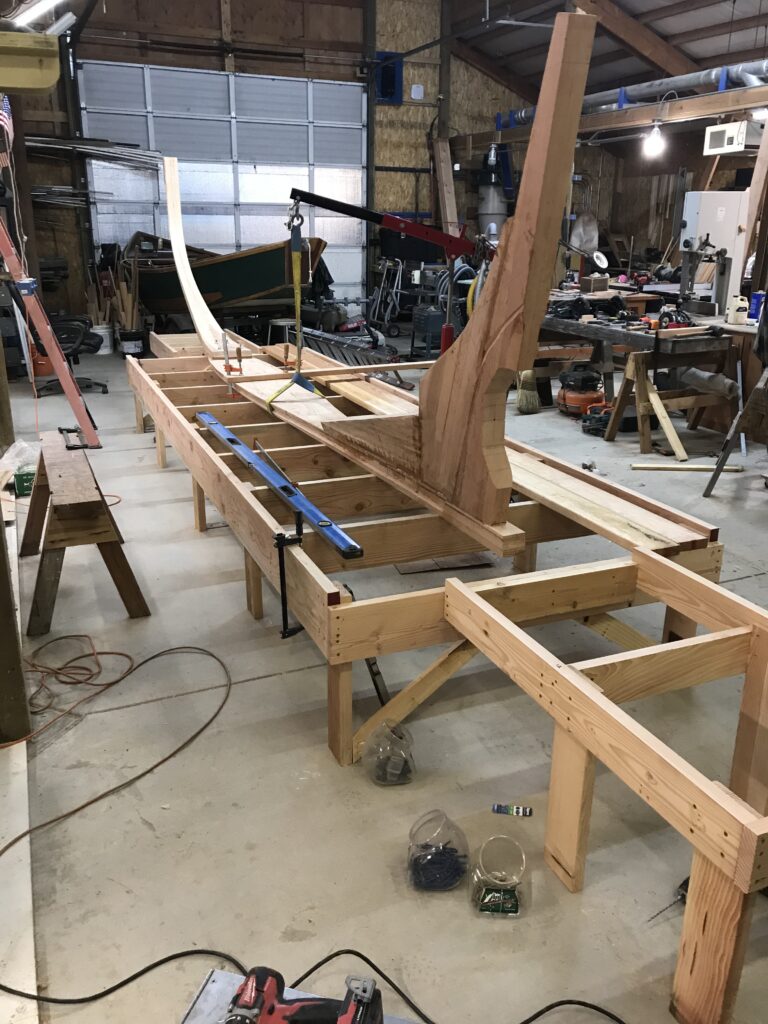

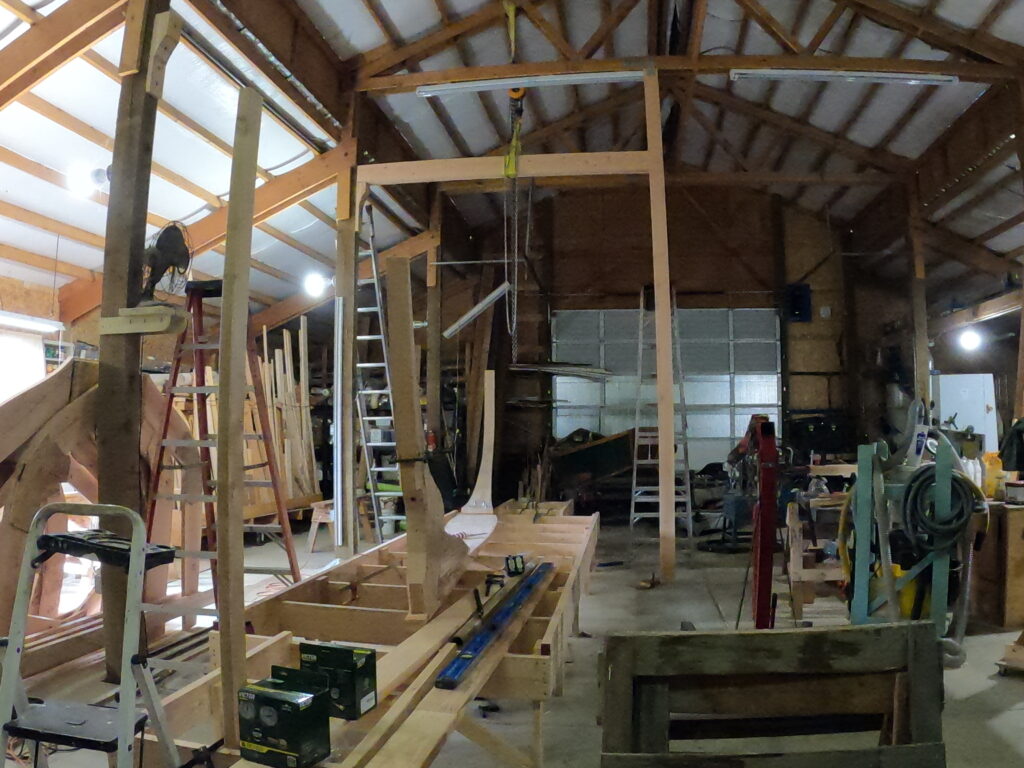
I began this month building the ladder frame or building jig on top of which I will build the hull upside down. My frame is fairly stout, squared to 1/16″ diagonally, leveled with a laser, cross braced and bolted to the floor. I think I could waltz an elephant across it. Once this was done, excitement began to build. For all of you who are boatbuilders, you know this. This is a big transition. No more crawling around on the floor with sticks and measuring things, pencils and pens sticking out of all my pockets. No more running around the shop in my socks, with lots of the sharp objects on the floor while traveling back and forth to the lofting. And no more worry about my lines fading. Yup, those fun days are over. From this point onward, I’ll be climbing up and over, around and through an actual boat. I have even bravely taken up some of the lofting floor to make room. Where all my stem rabbet profiles were painstakingly drawn sits a new table. One can’t have too many tables. The next picture shows Theresa being pulled, shoved, pried over to the building jig. I’m calling it the operating table. And there she sits on top, awaiting various procedures. So far, the backbone structure weighs 325 lbs.(147kgs) and the engine hoist is a huge help. The 2×4 clamped on is my preventer as the structure is pretty top heavy and tipping would cause significant chaos. In my shop there are two 6×8 posts next to the building frame exactly 12’ apart. The frame is positioned so that lifting points at stations 4 and 10 are directly in line with these posts. From these posts across to other posts I have erected 6×8 beams on which hang two 3 ton chain hoists in order to lift the whole assembly 13’ high and invert it. Once this is braced and tied off, I can erect the 12 station molds (already made) then lower the keel assembly on top of all of that. Sorry, no pictures of this yet as it hasn’t actually happened but when it does there will be drama and possibly a tear of relief.