Well here she sits, high and proud on her operating table. I say hello as I flip on the lights and head to the big door. She is now inverted, keel up, looking down at her many forms over which will flow her 48 or so oak frames and then planking. Quite an interesting shape, I think. As I sit in my shop chair and contemplate my next maneuvers, it occurs to me that this could be the first time that this exact shape has ever been seen by anyone, ever. Probably so, as the original Theresa was not built inverted and probably never flipped over. Amazing, as old as the world is, there can still be a first for something. A month ago, the backbone was all in pieces. Now it is all bedded and bronze bolted. Then I built the ladder frame. She then climbed up on her table and awaited my assistance in hoisting her up. I strapped both chain hoists on at stations 4 and 10 and proceeded to turn her on her side. But as I got to a certain point I realized: Holy Cow! I could easily loose it if I’m not careful.
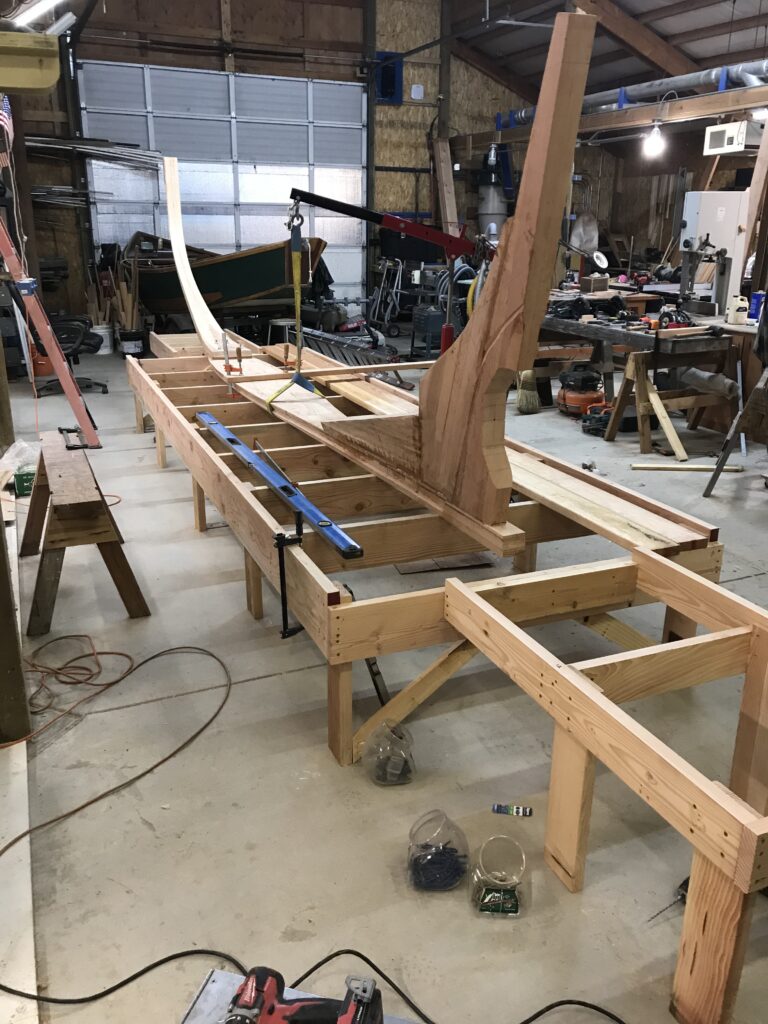
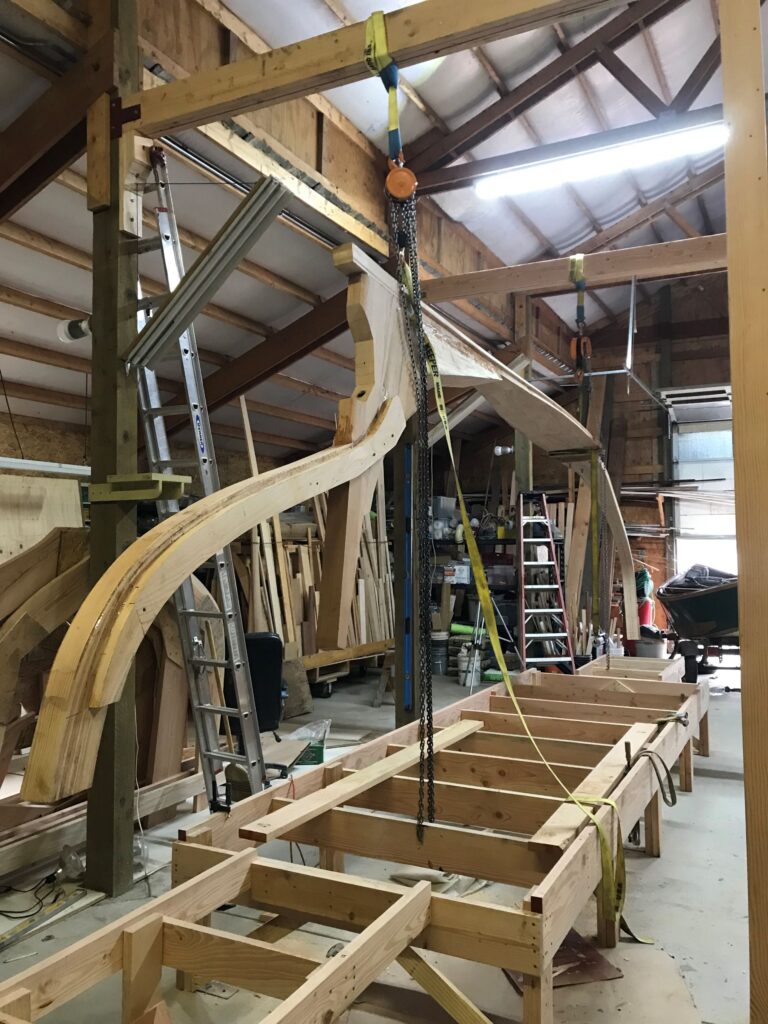
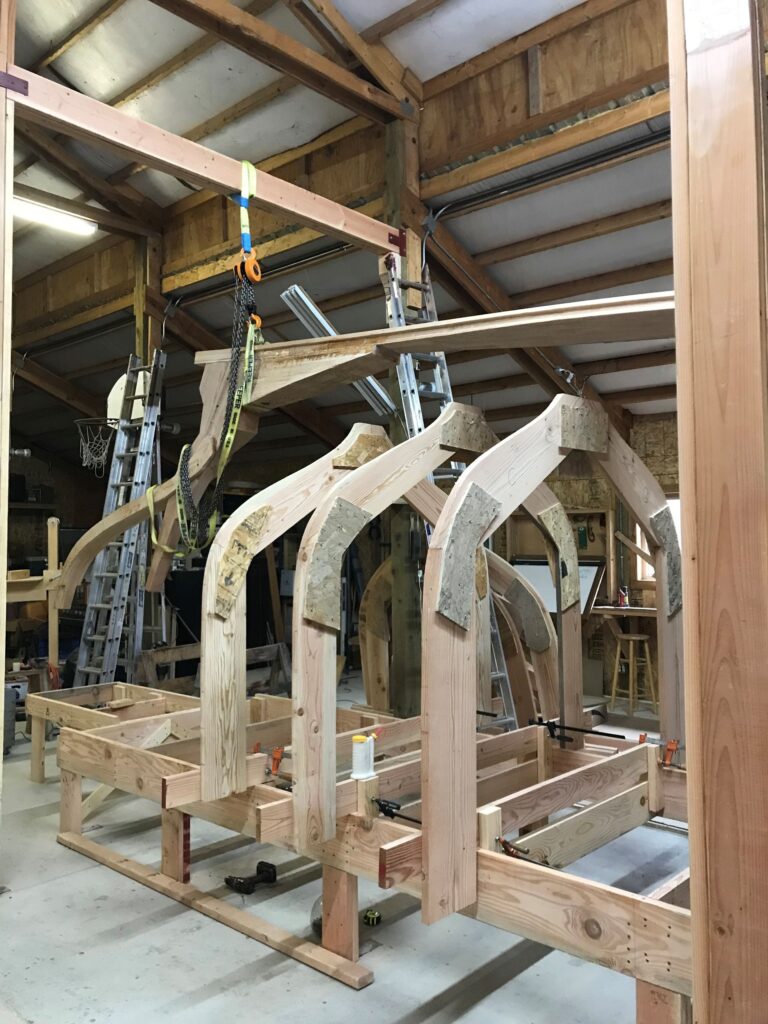
It seems, I’ve been told, I have this chronic, “one-man-bandness” condition. The symptoms are broken bones, aches and pains, bruises, etc. My wife keeps telling me I need to recognize the situation and call for help. She is much smarter than me. So I called my friend John and we got her flipped. And up she went. It was easy.
Once she was up and out of the way I began to slide the station mold forms onto the table (the strongback/ ladder frame etc.) being sure to get the form on the right side of the line. These are all in except #3 and #10. Three needs an extension, oops. And ten connects onto the knee after the keel is lowered.
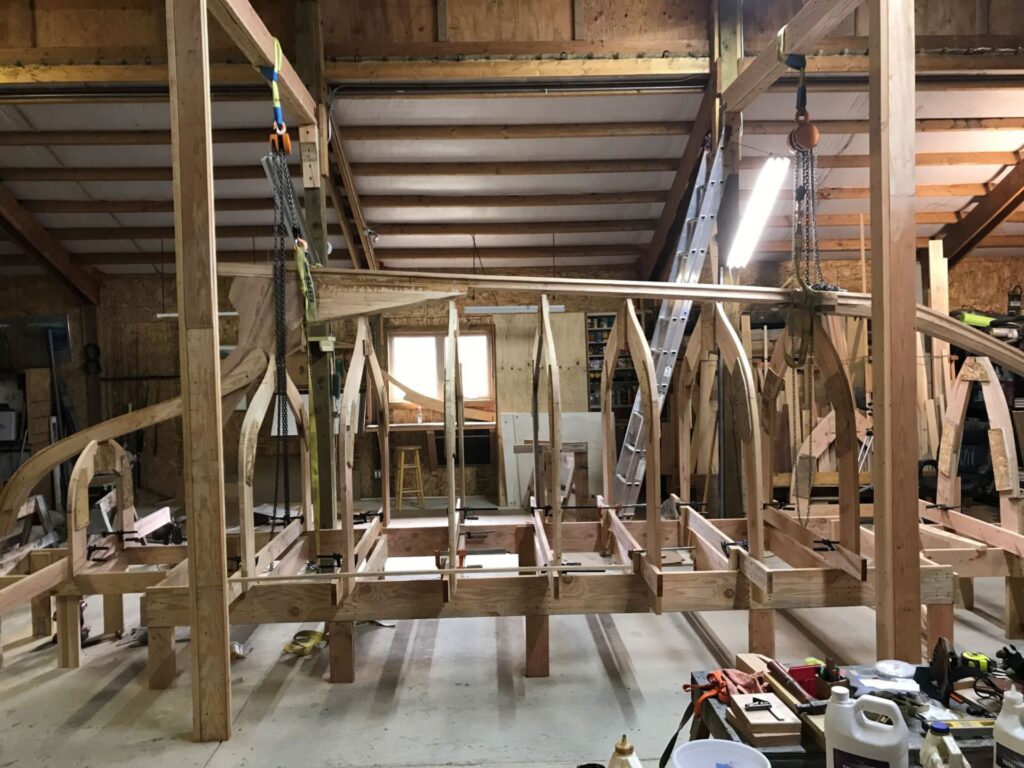
So my business now is with pushing, pulling, prying and stabilizing all these parts so I can actually build a boat over them. On sitting there, I soon realized how clever I was in the way I positioned the strongback adjacent to the two big posts in the shop. The two cranes I built (shown in the picture) will pick up the keel at points almost equidistant from each end. When lowered, the stem will sit on a ledge just outside the front 2×8 cross piece and be supported there. The tip of the horn timber will sit similarly and be supported off the aft 2×8 on the frame. The height of the frame is set so I can easily crawl under it and stand up. But here’s the best part. I suspect that the most difficult part of the hull to plank (and the most beautiful part of the boat) will be the canoe stern. This part of the hull will be about chest high, and I’ll be looking right at it. And the music continues. The four posts of the crane form a square about 12’x12’ with the beams about 14’ high. This allows me to lift the entire hull another 3’ and turn it within this space. Once upright I can lift it again to position the lead ballast under it.
While I was sitting there, raptured by all this euphoric haze about my cleverness, I am sobered by the crushing amount of work ahead. And so off I go, picking up my screw gun, hammer and apron to see if I can plow on just a little bit more in a forward direction.
What fun this is.
Dave Ahrens